5 kroków do wybudowania efektywnej hali produkcyjnej
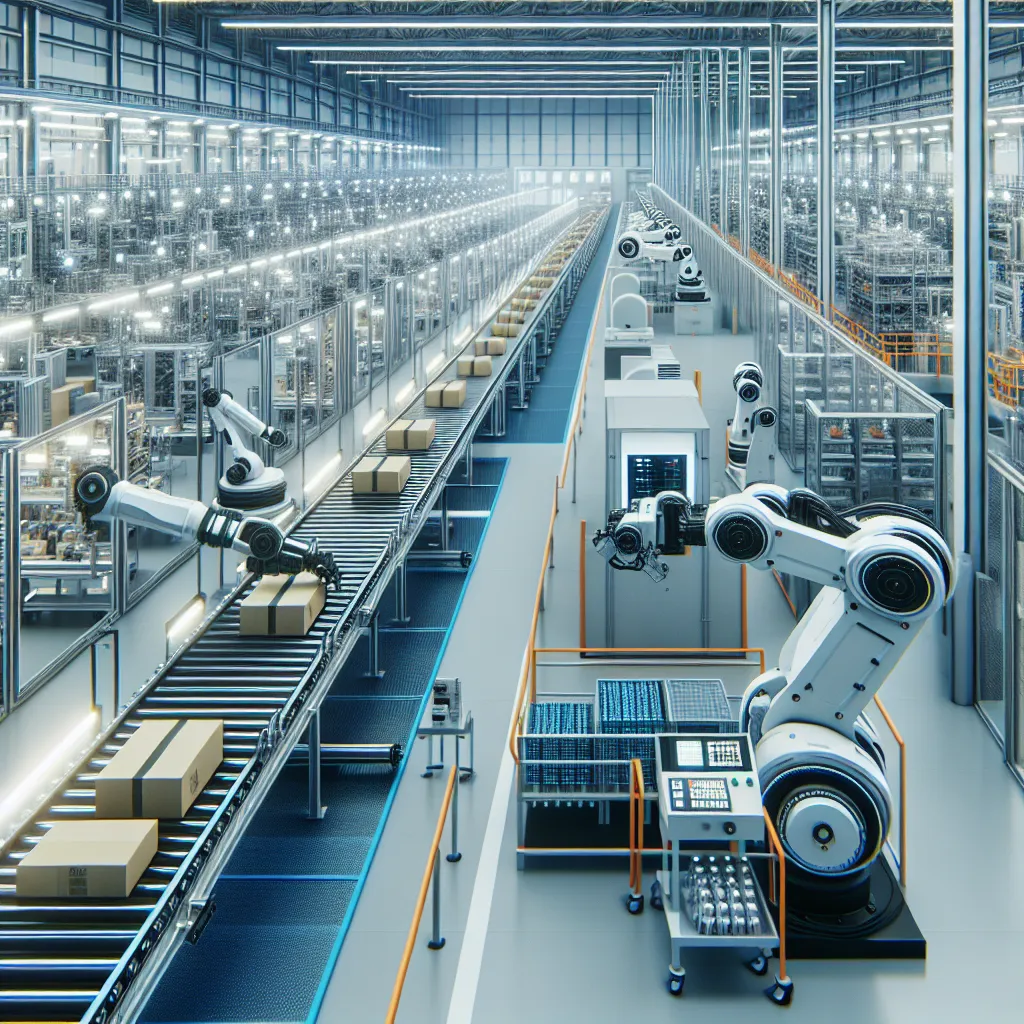
Planowanie efektywnej przestrzeni produkcyjnej
Podstawą wybudowania efektywnej hali produkcyjnej jest planowanie efektywnej przestrzeni produkcyjnej. Bez odpowiedniego zaplanowania przestrzeni, działalność produkcyjna może napotkać wiele problemów, takich jak zator produkcji, ograniczenia logistyczne czy niewłaściwe wykorzystanie powierzchni.
Aby osiągnąć sukces w budowie hali produkcyjnej, kluczowym krokiem jest dokładne planowanie przestrzeni produkcyjnej, uwzględniające wszelkie specyficzne wymagania branżowe oraz logistyczne. Skuteczne zarządzanie przestrzenią produkcyjną wiąże się z optymalizacją procesów zachodzących w hali, co przekłada się na efektywność i rentowność przedsięwzięcia.
Ważnym aspektem jest również odpowiedni dobór rozwiązań technologicznych i infrastruktury, które umożliwią optymalne wykorzystanie przestrzeni produkcyjnej, zgodne z obowiązującymi standardami oraz wytycznymi dotyczącymi bezpieczeństwa i ergonomii pracy.
Dlatego, aby dowiedzieć się więcej na temat budowy hali produkcyjnej, warto zapoznać się z ofertą budowa hali firmy AMWIN, która oferuje kompleksowe rozwiązania w zakresie budowy hal produkcyjnych.
Planowanie efektywnej przestrzeni produkcyjnej
Planowanie efektywnej przestrzeni produkcyjnej stanowi kluczowy krok w procesie wybudowania efektywnej hali produkcyjnej. Przestrzeń produkcyjna powinna zostać zaprojektowana w taki sposób, aby zapewniała optymalne warunki dla przepływu produkcji oraz wydajność procesów. Istnieje kilka istotnych kroków, które należy podjąć w celu zaplanowania efektywnej przestrzeni produkcyjnej.
Pierwszym krokiem jest analiza potrzeb produkcyjnych. Wymaga to zrozumienia rodzaju produkcji, ilości produkowanych jednostek oraz przepływu materiałów w procesie produkcyjnym. Na tej podstawie można określić niezbędną powierzchnię produkcyjną oraz rozmieszczenie poszczególnych stref, takich jak strefa przeładunku, montażu czy magazynowania.
Kolejnym istotnym aspektem jest optymalizacja układu przestrzennego. Poprawne rozmieszczenie poszczególnych stanowisk pracy, maszyn oraz obszarów składowania materiałów wpływa bezpośrednio na efektywność procesu produkcyjnego. Dobrze zaplanowana przestrzeń pozwala na skrócenie czasu potrzebnego na przemieszczanie się pracowników i materiałów oraz minimalizuje ryzyko zakłóceń w przepływie produkcji.
Kolejnym krokiem jest uwzględnienie przepisów i standardów bezpieczeństwa. Planując przestrzeń produkcyjną, należy zwrócić uwagę na zachowanie odpowiednich odległości między maszynami, zapewnienie dostępu do sprzętu gaśniczego oraz wyznaczenie ewakuacyjnych dróg bezpieczeństwa. Bezpieczeństwo pracowników i zgodność z przepisami stanowią istotny element efektywnego planowania przestrzeni produkcyjnej.
Następnie, kluczowe jest zastosowanie odpowiednich rozwiązań technologicznych i infrastrukturalnych. Obejmuje to wybór odpowiednich systemów oświetleniowych, wentylacyjnych, a także zastosowanie specjalistycznych rozwiązań takich jak suwnice czy systemy transportu wewnętrznego. Odpowiednia infrastruktura zapewnia sprawną pracę maszyn oraz komfortowe warunki dla pracowników, co przekłada się bezpośrednio na efektywność produkcji.
Ostatnim, lecz nie mniej istotnym krokiem, jest ciągła optymalizacja przestrzeni produkcyjnej. Proces produkcyjny oraz wymagania rynkowe mogą ulegać zmianom, dlatego istotne jest monitorowanie i ocena wydajności przestrzeni produkcyjnej w celu wprowadzenia ewentualnych korekt czy ulepszeń. Dzięki ciągłej optymalizacji, hala produkcyjna będzie mogła utrzymać wysoką efektywność na dłuższą metę.
Optymalizacja przepływu produkcji w hali produkcyjnej
Wybudowanie efektywnej hali produkcyjnej wymaga uwzględnienia wielu aspektów, w tym optymalizacji przepływu produkcji. Optymalizacja przepływu produkcji w hali produkcyjnej jest kluczowym elementem zapewnienia efektywności i rentowności procesów produkcyjnych. Istnieje wiele kroków, które mogą zostać podjęte w celu optymalizacji przepływu produkcji w hali produkcyjnej, a pięć z nich szczególnie warto uwzględnić.
Pierwszym krokiem do optymalizacji przepływu produkcji jest analiza istniejącego układu przestrzennego hali produkcyjnej. Konieczne jest zrozumienie aktualnego stanu przepływu materiałów oraz pracowników, identyfikacja bottlenecków i obszarów, które wymagają poprawy. Dzięki temu można opracować plan optymalizacji przestrzennej, który uwzględni zoptymalizowany układ maszyn, stanowisk pracy i szlaków komunikacyjnych.
Kolejnym krokiem jest zastosowanie metod lean manufacturing, takich jak 5S czy kanban, w celu usprawnienia przepływu produkcji. Eliminacja nadmiaru, uporządkowanie miejsca pracy, standaryzacja procesów i wizualne zarządzanie produkcją mogą znacząco zredukować marnotrawstwo czasu i zasobów oraz usprawnić przepływ materiałów.
Trzeci krok to wykorzystanie odpowiednich technologii, takich jak systemy automatyzacji, identyfikacji i śledzenia materiałów, które mogą usprawnić zarządzanie przepływem produkcji. Dzięki zastosowaniu nowoczesnych rozwiązań technologicznych można skrócić czasy przestoju maszyn, zwiększyć przepustowość oraz usprawnić monitorowanie i zarządzanie produkcją.
Kolejnym istotnym aspektem jest optymalizacja logistyki wewnętrznej, obejmująca planowanie tras materiałów, optymalizację magazynowania oraz zastosowanie właściwych rozwiązań transportowych w hali produkcyjnej. Efektywna logistyka wewnętrzna ma kluczowe znaczenie dla płynności przepływu produkcji.
Ostatnim, ale nie mniej istotnym krokiem jest ciągłe monitorowanie, analiza danych oraz wprowadzanie usprawnień. Dzięki regularnemu śledzeniu wskaźników wydajności, identyfikowaniu nowych obszarów poprawy oraz wprowadzaniu innowacji, można utrzymać optymalizację przepływu produkcji na stałym, wysokim poziomie.
Podsumowując, optymalizacja przepływu produkcji w hali produkcyjnej wymaga zintegrowanego podejścia, uwzględniającego zarówno organizację przestrzenną, metodologie produkcji, nowoczesne technologie, logistykę wewnętrzną, jak i ciągłe doskonalenie. Tylko poprzez kompleksowe podejście można osiągnąć efektywność i rentowność procesów produkcyjnych.
Wybór odpowiedniego wyposażenia i narzędzi produkcyjnych
Wybór odpowiedniego wyposażenia i narzędzi produkcyjnych jest kluczowym krokiem w budowie efektywnej hali produkcyjnej. Przed podjęciem decyzji warto przeprowadzić dokładną analizę potrzeb i wymagań produkcyjnych. Po pierwsze, należy zidentyfikować procesy produkcyjne, które będą wykonywane w hali, a następnie określić odpowiednie narzędzia i maszyny do ich realizacji. W kolejnym kroku warto skoncentrować się na wyszukaniu dostawców, którzy oferują wysokiej jakości i nowoczesne wyposażenie produkcyjne. Przy wyborze maszyn i narzędzi warto zwrócić uwagę na ich parametry techniczne, wydajność, rekomendacje dotyczące serwisu oraz ewentualne wsparcie techniczne ze strony dostawcy. Kolejnym istotnym krokiem jest analiza kosztów eksploatacji maszyn oraz ich wpływ na efektywność procesów produkcyjnych. Wreszcie, nie należy zapominać o zapewnieniu odpowiedniego szkolenia dla personelu, który będzie obsługiwał nowe narzędzia i maszyny. Poprawnie dobrany sprzęt produkcyjny może znacząco wpłynąć na wydajność i jakość produkcji w hali produkcyjnej, dlatego warto poświęcić mu wystarczająco dużo uwagi podczas planowania nowej hali produkcyjnej.
Doskonalenie procesów logistycznych w hali produkcyjnej
Procesy logistyczne odgrywają kluczową rolę w efektywnym funkcjonowaniu hali produkcyjnej. Doskonalenie tych procesów może przynieść znaczne korzyści w postaci zwiększenia wydajności, redukcji kosztów oraz optymalizacji przepływu materiałów i produktów. Oto 5 kluczowych kroków, które należy podjąć w celu doskonalenia procesów logistycznych w hali produkcyjnej.
- Analiza struktury przestrzennej hali: Pierwszym krokiem do efektywnego doskonalenia procesów logistycznych jest analiza struktury przestrzennej hali produkcyjnej. Poprawna organizacja przestrzeni, umiejscowienie stref składowania, stacji roboczych i wyjść dla produktów ma kluczowe znaczenie dla płynności procesów logistycznych.
- Implementacja systemu identyfikacji i śledzenia: Wdrażanie systemu identyfikacji towarów (np. za pomocą kodów kreskowych, RFID), a także systemu śledzenia (np. za pomocą oprogramowania do zarządzania magazynem) umożliwia dokładną lokalizację produktów w hali produkcyjnej, co przyspiesza ich transport i przepływ przez halę.
- Optymalizacja układu komunikacyjnego: Poprawa komunikacji między strefami produkcyjnymi, magazynowymi i obszarami załadunku oraz wyładunku jest kluczowa dla efektywności procesów logistycznych. Dobrze zaprojektowany układ komunikacyjny przyspiesza przepływ materiałów i gotowych produktów.
- Automatyzacja procesów magazynowych i transportowych: Wprowadzenie automatyzacji w procesach składowania, kompletacji zamówień oraz transportu wewnętrznego pozwala na zwiększenie wydajności, redukcję błędów oraz optymalizację czasu realizacji zleceń.
- Monitorowanie i analiza danych logistycznych: Ostatnim krokiem jest wprowadzenie systemu monitorowania oraz analizy danych logistycznych. Pozwoli to na ciągłe doskonalenie procesów poprzez identyfikację obszarów wymagających optymalizacji oraz umożliwi bieżące podejmowanie decyzji poprawiających funkcjonowanie hali produkcyjnej.
Skuteczne doskonalenie procesów logistycznych w hali produkcyjnej wymaga podejścia zintegrowanego, uwzględniającego aspekty praktyczne, technologiczne i organizacyjne. Dzięki zastosowaniu powyższych kroków możliwe jest zwiększenie efektywności działania hali produkcyjnej, co w konsekwencji prowadzi do poprawy wyników finansowych oraz zadowolenia klientów.